Custom LED Lamps
Challenge
Our client had provided basic art direction for almost 300, twenty foot tall lighted art obelisks which would be installed along 1.7 miles os busy urban boulevard. The art object design was a tall, vertical, complex double helix, tapered with an elliptical footprint. They were to be constructed from eight 1.5’ custom stainless steel tubing with 300 individually controllable LED lamps covering the framework. These lighting form factors didn’t exist. The lamps themselves were to be surface mounted somehow, in a way so as to beautifully integrate them with the tube, while displaying the faceted lens like a jewel setting. So we were challenged with developing these custom tube-mounted LED pixels…which would have be interconnected to custom made control systems for delivering a choreography to make 300 art obelisks dance in unison. We would be using the shaped tubes as conduit for the data and electric cables connecting to power and control sources in the base of the obelisk.
​
Solution
The pixel lamps themselves were to be faceted to look like cut crystal. The base of the lamp would require waterproof mounting to 1.5” diameter tubing which was pierced to allow the data and power wires from the lamp to be routed through the tube without being visible from the outside. The lamps had to be removeable and replaceable so we developed several 3D lamp iterations and attachment methods. The parts were 3D printed to test fitment and assembly methods. Finally we landed on a custom molded, polycarbonate lamp base which was designed to saddle the tube. The parts were tooled and custom molded specifically for this application. The contact area was sealed utilizing a highly-specialized closed-cell UHB foam tape which was determined to compatible with both stainless steel and polycarbonate. The tape we selected is commonly used to assemble the chassis of super cars. It was expensive but had amazing holding and sealant powers. The full adhesive property could only be achieved by exerting enough pressure to extrude the sticky component of the tape into the micro-pores of both dissimilar materials. This was accomplished by adding two internal self tapping screws which pulled the parts together, providing a watertight seal, and fully activating the adhesive properties of the UHB foam mastic. Ultimately the effect was magical. Our client love it, but really never realized the innovation and resourcefulness required to make it all work.

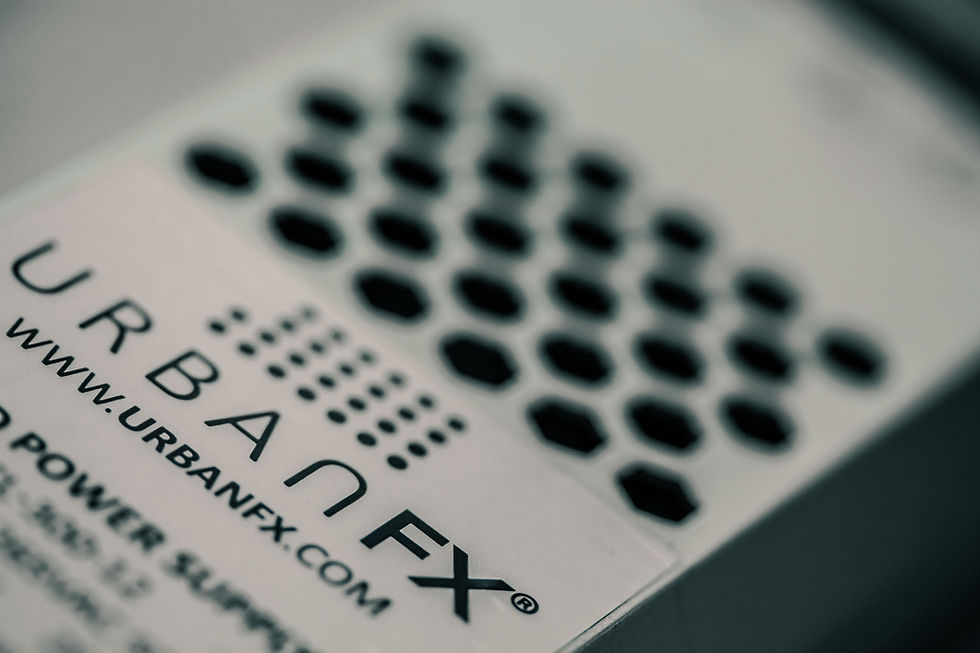

