Make a Hole!
Challenge
We landed a lighting and metal fabrication project requiring us to drill 270,000 precision located holes through the curved outer surface of work hardened stainless steel tubing. This is an almost impossible task utilizing traditional hole drilling methods. Stainless steel can be extremely difficult to drill, because as it is being drilled, the developing hole is simultaneously hardening and generating heat, which destroys expensive drill bits. Anyone who has drilled into the curved exterior of small diameter tube understands the difficulty of constraining the bit. It wants to walk, making it very difficult to hold the location. This particular job also had a requirement for holes in small spaces where there was no room for a drill motor, and there was no possibility of pre drilling holes prior to assembly. Needless to say, this was a very difficult challenge.
Solution
We had no choice but to invent a new solution the problem. A new way to drill holes. We experimented with a great number of possibilities and finally landed on the use of a mini-plasma cutter to torch the holes in the tubing. Our team developed a tube fixture to guide the tip of a mini plasma cutter which was used to hand-cut the 3 different hole sizes required. The solution created many other downstream issues which would need solutions also. The largest hole would leave slugs which dropped into the tube and had to be removed. We developed a process for that. The jet stream of heat from the plasma cutter would easily discolor the opposite side of the tube which would add labor and time to the process. But, the benefits of using our plasma drill were clear. The holes were required, in large measure, to receive self tapping screws. This was made easier because of the annealing effect of the heat from the plasma. The heat softened the stainless around the hole allowing our thread cutting screws to work much better.

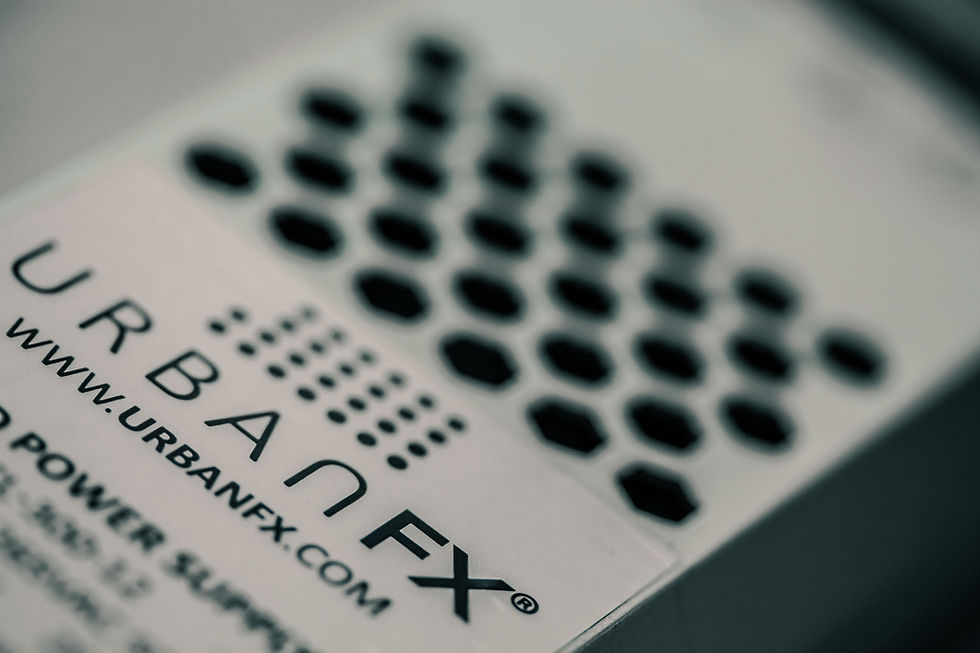

